Wszystko, co należy wiedzieć o uchwytach tokarskich
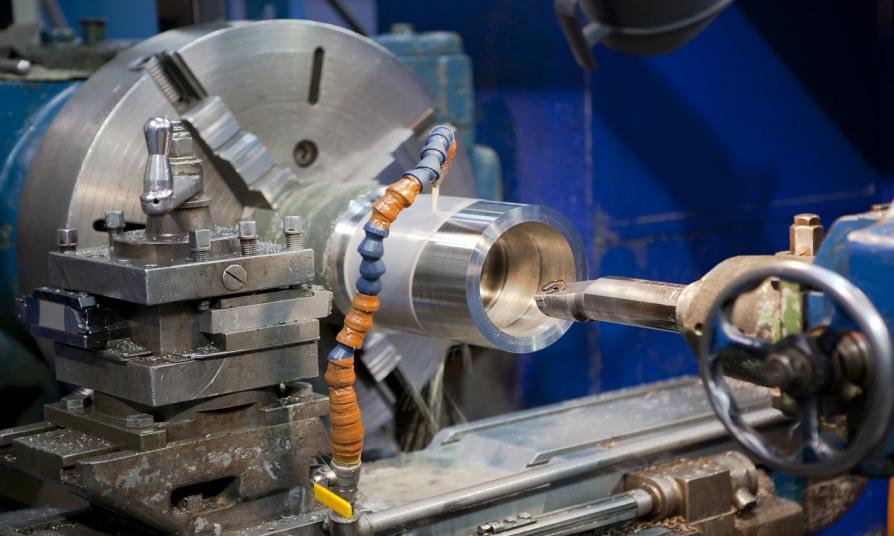
Toczenie jest jednym z najczęściej stosowanych rodzajów obróbki metalu. Możliwość wykonania detalu na tokarce z odpowiednią precyzją zależy od wypadkowej działania wielu elementów, jedną z najważniejszych ról odgrywa jednak uchwyt tokarski, który jest odpowiedzialny za unieruchomienie i pozycjonowanie przedmiotu obrabianego podczas pracy. Jego stabilność oraz prawidłowe działanie są więc warunkiem utrzymania właściwych parametrów.
Na czym polega toczenie i jaką funkcję pełnią uchwyty tokarskie?
Elementy maszyn i urządzeń pracują zwykle pod dużymi obciążeniami, zarówno jeśli chodzi o oddziałujące na nie siły, jak i prędkości, z jakimi się poruszają czy temperaturę, jakiej wpływowi są poddawane. Większość z nich jest więc wykonywana ze stopów różnych metali, a do prawidłowego realizowania swoich zadań muszą charakteryzować się nie tylko wysoką wytrzymałością mechaniczną, ale również dużą precyzją. Na ogół wśród podstawowych wymagań znajdzie się odpowiednia tolerancja wymiarowa, pozwalająca na eliminowanie ryzyka powstawania luzów między poszczególnymi częściami, a także właściwy poziom chropowatości, który ma wpływ na generowane opory oraz wielkość tarcia. Do zapewnienia oczekiwanego poziomu najważniejszych parametrów używane są przede wszystkim różne metody obróbki wiórowej. Są one dobierane w zależności od charakterystyki gotowego wyrobu oraz kształtu, jaki ma zostać uzyskany. Do najczęściej wykorzystywanych należy m.in. toczenie – wyjaśnia przedstawiciel firmy APM MORKOM, specjalizującej się w sprzedaży elementów urządzeń CNC oraz podzespołów automatyki przemysłowej.
Toczenie polega na obróbce ubytkowej, prowadzącej do powstania elementu, który ma mieć kształt będący odzwierciedleniem bryły obrotowej powstałej przez rotację dowolnej płaskiej figury geometrycznej. Materiał, z którego ma być wytworzony detal, jest wprawiany w ruch obrotowy, a jego zbędny naddatek jest usuwany za pomocą narzędzia w postaci noża tokarskiego, który może poruszać się wzdłuż osi obrotu, a także zbliżać do niej podczas toczenia, czyli obróbki powierzchni zewnętrznej albo oddalać, jeżeli wykonywane jest wytaczanie, a zatem obróbka kształtowa powierzchni wewnętrznej. Właściwa geometria będzie uzyskiwana albo w wyniku doboru ścieżki, po której porusza się nóż tokarski w ramach obróbki punktowej, albo powstanie jako rezultat ukształtowania krawędzi tnącej narzędzia w obróbce kształtowej.
Choć forma przedmiotu obrabianego uzyskiwana podczas toczenia zależy w głównej mierze od ruchu narzędzia, to równie ważne jest precyzyjne ustalenie jego położenia oraz stabilne mocowanie. Jest to o tyle istotne, że wszystkie parametry ruchu głowicy roboczej są określane w odniesieniu do pozycji przedmiotu obrabianego, jeśli nie będzie ona wystarczająco precyzyjnie ustawiona, wymiary gotowego wyrobu nie będą odpowiadały tym, jakie zostały założone w projekcie. Do wykonania niezbędnych zadań obróbkowych każdy przedmiot obrabiany musi być pozbawiony odpowiedniej liczby stopni swobody, czyli możliwości przemieszczania się w jednej z trzech płaszczyzn trójwymiarowego układu współrzędnych – X, Y, Z, a także obrotu w osiach znajdujących się w ich obrębie. Ze względu na specyfikę toczenia wymagającego wykonywania przez przedmiot obrabiany wyłącznie ruchu obrotowego jego ustalenie odbywa się przy zastosowaniu uchwytów odbierających 5 stopni swobody.
Samocentrujące szczękowe uchwyty tokarskie i ich zastosowanie
W klasycznej tokarce obróbka jest możliwa za sprawą obrotów wrzeciona, które wprawia w ruch przedmiot obrabiany rotujący w wybranej osi. Przedmiot obrabiany jest na ogół ustalany przy wykorzystaniu pary kłów – jeden z nich znajduje się we wrzecionie tokarki, drugi w tzw. koniku, będący elementem ruchomym, przesuwającym się wzdłuż osi obrotu wrzeciona, co daje możliwość mocowania przedmiotów o różnej długości. Dwa stabilne punkty podparcia w postaci kłów wymagają wykonania w przedmiocie obrabianym tzw. nakiełków, czyli dwóch nawiercanych stożkowatych otworów, wyznaczających oś obrotu. Przedmiot obrabiany jest wprawiany w ruch za sprawą tzw. zabieraka mocowanego do jego obwodu i połączonego z tarczą zabierakową. Obróbka jest prowadzona dzięki przemieszczaniu się suportu tokarki, na którym w odpowiednim imaku umieszczane są noże tokarskie.
Największe możliwości, jeśli chodzi o mocowanie różnych rodzajów przedmiotów obrabianych, dają uchwyty szczękowe. Elementem mocującym, który bezpośrednio unieruchamia przedmiot obrabiany, są w tym przypadku szczęki, zaciskające się i jednocześnie centrujące materiał. Jest to możliwe za sprawą układu składającego się z tarczy ze spiralnymi rowkami będącymi spiralą Archimedesa. Ponieważ na dolnych częściach szczęk są wykonane odpowiednie wyżłobienia, ruch tarczy powoduje równomierne zsuwanie się lub rozsuwanie szczęk, które przemieszczają się promieniowo. Przesuw może być również realizowany za sprawą układu zębatek – w takim przypadku ruch promieniowy szczęk jest osiągany wyniku istnienia właściwych połączeń mechanicznych i również sterowny centralnie dzięki jednej zębatce powodującej przesuniecie pozostałych elementów. Inną możliwością jest stosowanie w uchwytach tokarskich niezależnego przesuwu każdej szczęki za pomocą oddzielnego układu zębatek przy jednoczesnym zachowaniu opcji ustawiania szczęk synchronicznie przy użyciu spirali Archimedesa. Takie rozwiązanie pozwala na obróbkę elementów o złożonej geometrii i wielu osiach symetrii. Uchwyty tego rodzaju są nazywane uchwytami kombinowanymi.
Uchwyty mogą występować w wersjach z różną ilością szczęk w zależności od specyfiki mocowanego przedmiotu. Uchwyty dwuszczękowe są na ogół używane do pozycjonowania elementów, które wprawdzie mają oś symetrii zgodną z osią obrotu, jednak ich powierzchnia ma postać płaszczyzn np. w przypadku prętów o profilu kwadratowym lub sześciokątnym. Najczęściej używane i zarazem uniwersalne są uchwyty trójszczękowe, które znakomicie mocują wszelkiego rodzaju elementy o przekroju okrągłym. Oferowane są także uchwyty czteroszczękowe o zastosowaniu podobnym do dwuszczękowych, a nawet sześcioszczękowe, które zazwyczaj stosuje się do obróbki elementów cienkościennych, co pozwala na optymalne rozłożenie sił działających na ich powierzchnię podczas skrawania.
Korzystanie z uchwytów samocentrujących wymaga często dopasowywania rodzaju wykorzystywanych szczęk do typu obrabianego materiału. Standardowym rozwiązaniem podczas obróbki zgrubnej oraz pracy z materiałami o wysokiej wytrzymałości jest stosowanie szczęk twardych. W przypadku, gdy w grę wchodzi jednak skrawanie przedmiotów, które mają być wykonane ze stopów bardziej podatnych na zarysowania albo wówczas, gdy obrabia się elementy cienkościenne, które mogą ulec deformacji, używa się szczęk miękkich. Mogą one być wykonane ze stali, aluminium lub nawet tworzywa sztucznego. Szczęki miękkie są zazwyczaj dostosowywane do kształtu powierzchni przedmiotu obrabianego np. przez odpowiednie wyprofilowanie ich powierzchni.
Uchwyty trzpieniowe i tulejowe
Poza uchwytami szczękowymi do ustalania i mocowania przedmiotów obrabianych stosuje się również inne konstrukcje. Do bardzo popularnych należą uchwyty trzpieniowe oraz tulejowe. Uchwyty trzpieniowe wykorzystuje się do obróbki elementów, które posiadają otwory wewnętrzne powstałe podczas wytaczania – np. takich jak tarcze, cylindry czy tuleje. Używa się ich na ogół do obróbki wykańczającej, która ma na celu dopracowanie ich powierzchni zewnętrznej. Podstawowe rodzaje uchwytów trzpieniowych to uchwyty stałe lub rozprężne. W przypadku tych pierwszych mocowanie następuje dzięki wciśnięciu przedmiotu obrabianego na trzpień. W uchwytach rozprężnych przedmiot obrabiany jest mocowany za sprawą docisku elementów powierzchni trzpienia napierających na jego wewnętrzne ścianki. Mechanizm rozprężny może wykorzystywać tuleję rozprężną, która jest wciskana na stożek, dzięki czemu zwiększa swoją objętość. W niektórych przypadkach używane są także sprężyny krążkowe czy dociskane do powierzchni wałeczki. Stosuje się też trzpienie walcowe, na których umieszcza się elementy obrabiane za pomocą pasowania oraz dociska powierzchniami czołowymi.
Uchwyty tulejowe do tokarek są przeznaczone do obróbki elementów o powierzchniach walcowatych o niezbyt dużych średnicach. W tym przypadku są osadzane wewnątrz uchwytu, stosuje się je więc m.in. do obróbki wałków i prętów. Podobnie jak w przypadku trzpieni wykorzystuje się równe rozwiązania umożliwiające unieruchomienie przedmiotu obrabianego. Do najprostszych metod blokowania należą wszelkiego rodzaju konstrukcje z mocowaniami zaciskającymi się na powierzchni elementu obrabianego. Mogą to być tuleje zaciskowe dociskane za pomocą sprężyn, gwintu lub schodzących się klinów. Stosowane są także mechanizmy kulkowe.
Uchwyty tokarskie są jednymi z ważniejszych elementów przesądzających o dokładności obróbki. Muszą zapewniać nie tylko odpowiednią stabilność i możliwość wprawiania w ruch przedmiotu obrabianego, ale także odpowiadać jego rodzajowi i wymiarom. Sposób mocowania ma również duże znaczenie dla tempa, w jakim można wymieniać kolejne obrabiane detale.
Dziękujemy za ocenę artykułu
Błąd - akcja została wstrzymana
Polecane firmy
-
-
-
Kwiaciarnie
Małgorzata Kwiaciarnia Małgorzata Borek
woj. dolnośląskie55-200 Oława, Iwaszkiewicza 137A
-